热门搜索
- 奥迪纯电
- 奥迪高性能车
- 购车工具
- SQ7
- A8L Horch 创始人版
您使用 "" 找到了 条结果
热门搜索
- 奥迪纯电
- 奥迪高性能车
- 购车工具
- SQ7
- A8L Horch 创始人版
您使用 "" 找到了 条结果
为了给您更好的用户体验,我们正在使用Cookie技术。继续浏览本网站即表示您同意我们使用Cookie。您可以在浏览器设置中更改此设置。若想了解更多,可阅读我们的Cookie政策。
隐私政策
本政策仅适用于一汽-大众汽车有限公司 (以下统称“我们”或“一汽奥迪官方网站”)的网站服务。
隐私政策更新日期:2020年8月5日
隐私政策版本号: 2.0.1
一汽-大众汽车有限公司 (以下统称“我们”或“一汽奥迪官方网站”) 是一家注册地址为【吉林省长春市安庆路5号】的公司。我们非常重视您的个人信息和隐私保护。
本隐私政策旨在帮助您了解我们会收集哪些数据、为什么收集这些数据、会利用这些数据做什么以及我们如何保护这些数据。
1. 本隐私政策将依次向您说明我们可能收集的个人信息(部分功能可能需要收集个人敏感信息)范围、收集目的、收集方式,以及拒绝提供个人信息可能导致的结果。我们将严格遵循合法、正当、必要的原则,收集、使用用户信息。
2. 本隐私政策将向您说明我们如何保护个人信息安全、如何储存个人信息以及如何处理未成年人的个人信息。
3. 您可以通过本隐私政策所列途径访问、更正、删除您的个人信息,也可以通过投诉咨询、我要反馈等功能行使您的相关权益。
4. 我们将严格按照本隐私政策说明的场景使用或者共享您的个人信息,如果超出本隐私政策说明的范围,我们会再次向您告知并征得您的明示同意。
本政策包含以下内容:
一、 个人信息的定义及与范围;
二、 我们如何收集和使用您的个人信息
三、 我们如何使用Cookie和同类技术
四、 我们如何共享、转让、公开披露您的个人信息
五、 我们如何保存及保护您的个人信息
六、 您的权利
七、 我们如何处理未成年人的个人信息
八、 您的个人信息如何进行跨境转移
九、 适用法律与争议解决
十、 本政策如何更新
十一、如何联系我们
一、 个人信息的定义及与范围
个人信息,是指以电子或者其他方式记录的能够单独或者与其他信息结合识别自然人个人身份的各种信息,在本平台隐私政策中包括:基本信息(姓名、生日、性别、个人电话号码、电子邮箱);网路身份标识(个人信息主体账号、IP 地址、个人数字证书);个人教育工作信息(个人职业、职位、工作单位、学历);个人上网记录(网站内浏览记录、点击记录)。
个人敏感信息,是指一旦泄露、非法提供或滥用可能危害人身和财产安全,极易导致个人名誉、身心健康受到损害或歧视性待遇等的个人信息,在本平台隐私政策中包括:其他信息(系统账号、IP地址、邮箱地址及与前述有关的密码)
匿名化处理后的信息,即通过对个人信息的技术处理,使得个人信息主体无法被识别,且处理后不能被复原的信息,匿名化处理后的信息不属于个人信息。
其他无法识别特定自然人身份或者反映特定自然人活动情况的信息不属于个人信息。
以上“个人信息”、“个人敏感信息”“匿名化处理”定义及所包含内容出自于GB/T35273《个人信息安全规范》。
二、 我们如何收集和使用您的个人信息
我们会按照此隐私政策所述的以下业务功能、目的,收集和使用您的个人信息:
网站业务功能分为基本业务功能和扩展业务功能,我们将详细向您说明各业务功能收集的个人信息,收集的方法、目的和使用方法。
1. 基本业务功能需要收集和使用的个人信息
基本业务功能需收集和使用的个人信息主要指我们为您提供社交及车辆销售服务相关的核心基本功能所需的相关信息。您须提供此类信息才能使我们实现上述基本功能。如果您不提供相关信息,您可能将无法享受我们提供的产品/服务。
• 当您注册账号时,我们需要收集您的手机号码、密码,这些信息为了完成账号注册;
2.扩展业务功能需收集和使用的信息
扩展业务功能是“奥迪官方网站”为您提供的扩展功能或服务。是为了提供更好的产品或服务,或者改善我们产品或服务,从而提供一些扩展的业务功能,这些扩展功能会收集和使用您的个人信息。
如果您不提供或拒绝授权使用这些个人信息,我们可能无法提供对应的扩展功能服务,但不影响您使用“奥迪官方网站”的核心基本功能;
您可以通过各项扩展功能提供的方式,撤销相关个人信息使用的授权;
• 当您使用试乘试驾服务时,我们会收集您意向经销商、意向车型、意向时间的选择信息;将使用您意向经销商、意向车型、意向时间的选择信息、姓名、手机号码,并共享至您的意向经销商,意向经销商将与您联系并确定试乘试驾行程,及后续提供您所需的试乘试驾服务;
• 当您使用二手车-我要买车服务时,我们会收集您意向经销商、意向车型的选择信息;将使用您意向经销商、意向车型、意向时间的选择信息、姓名、手机号码,并共享至您的意向经销商,意向经销商将与您联系并提供您所需的二手车-我要买车服务;
• 当您使用二手车-我要卖车服务时,我们会收集您意向经销商、现有车型的选择信息;将使用您意向经销商、意向车型、意向时间的选择信息、姓名、手机号码,并共享至您的意向经销商,意向经销商将与您联系并提供您所需的二手车-我要卖车服务;
• 当您使用二手车-我要置换服务时,我们会收集您意向经销商、现有车型、意向车型的选择信息;将使用您意向经销商、意向车型、意向时间的选择信息、姓名、手机号码,并共享至您的意向经销商,意向经销商将与您联系并提供您所需的二手车-我要置换服务;
• 当您使用二手车-预约评估服务时,我们会收集您意向经销商、现有车型的选择信息;将使用您意向经销商、意向车型、意向时间的选择信息、姓名、手机号码,并共享至您的意向经销商,意向经销商将与您联系并提供您所需的二手车-预约评估服务;
• 当您使用获取经销商底价服务时,我们会收集您意向经销商、意向车型、意向时间的选择信息;将使用您意向经销商、意向车型、意向时间的选择信息、姓名、手机号码,并共享至您的意向经销商,意向经销商将与您联系并提供您所需的获取经销商底价服务;
• 当您使用索取车型手册服务时,我们会收集您车系、车型的选择信息;将使用您的意向车系、车型的选择信息、姓名、手机号码,并共享至您的意向经销商,意向经销商将与您联系并提供您所需的索取车型手册服务;
• 当您使用购车咨询服务时,我们会收集您意向经销商、意向车型、意向时间的选择信息;将使用您意向经销商、意向车型、意向时间的选择信息、姓名、手机号码,并共享至您的意向经销商,意向经销商将与您联系并提供您所需的购车咨询服务;
• 当您使用大用户购车服务时,我们会收集您意向车型、意向时间的选择信息;将使用您意向车型、意向时间的选择信息、姓名、手机号码,并共享至可以为您提供对应服务的相关机构,相关机构将与您联系并提供您所需的大用户购车服务;
• 当您使用落地页抽奖服务时,我们会收集您的姓名、电话、地址、意向经销商的选择信息;将使用您的姓名、电话、地址、意向经销商的选择信息,并共享至您的意向经销商,意向经销商将与您联系并提供您所需的相关服务;
• 改善我们的产品和服务,开展内部审计、数据分析和研究,您选择提供的反馈对帮助“奥迪官方网站”改进我们的产品或服务而言极为珍贵。为了跟踪您选择提供的反馈,“奥迪官方网站”可能会使用您所提供的个人信息与您联系,并保留记录。我们会使用收集的信息对产品或服务进行分析,以改进我们及关联方提供的产品或服务,并进行必要的业务运营,例如运营产品或提供服务,评估、维护和改进产品或服务的性能,开发新的产品和服务、提供客户支持等。
• 您接受并同意授权我们从一汽-大众的服务供应商、授权经销商、为您提供服务的社交媒体(平台)以及电信运营商等处(以下称“信息收集者”)获取您的其他个人信息(该等信息包括 基本信息(姓名、生日、性别、民族、住址、个人电话号码、电子邮箱);个人身份信息(身份证);网路身份标识(个人信息主体账号);个人教育工作信息(个人职业、职位、学历、学位);个人上网记录(网站浏览记录、软件使用记录、点击记录);个人常用设备信息(硬件序列号、设备MAC地址、唯一设备识别码)),您同意我们利用该等前述以及本文件中您同意我们搜集和获取的信息用于提高对您的产品或服务质量、用户体验以及我们所提供的产品或服务的推介活动。
3. 事先征得授权同意的例外
请注意:在以下情形中,收集、使用个人信息无需事先征得您的授权同意:
• 与国家安全、国防安全直接相关的;
• 与公共安全、公共卫生、重大公共利益直接相关的;
• 与犯罪侦查、起诉、审判和判决执行等直接有关的;
• 出于维护您或其他个人的生命、财产等重大合法权益但又很难得到本人同意的;
• 所收集的个人信息是您自行向社会公众公开的;
• 从合法公开披露的信息中收集个人信息的,如合法的新闻报道、政府信息公开等渠道;
• 根据您的要求向您提供产品或服务所必需的;
• 用于维护所提供的产品或服务的安全稳定运行所必需的,例如发现、处置产品或服务的故障;
• 法律法规规定的其他情形。
三、 我们如何使用Cookie和同类技术
3.1 我们使用 Cookie 、标签和脚本等同类终端收集和存储技术
• Cookie是支持服务器端(或者脚本)在客户端上存储和检索信息的一种机制。Cookie文件是一种很小的数据文件,这些文件会存储在您的计算机或移动设备上。
• 当您使用本网站时,我们可能会使用Cookie或者同类技术来收集和存储信息,这些信息可能与您的偏好或设备有关,通常不会用于直接识别您的身份。
• Cookie技术用于为使您获得更轻松安全的访问体验,改善产品服务及用户体验,或及时发现并防范安全风险,为您提供更好的服务。这些缓存信息主要包括用户个人配置信息、网站临时运行参数信息。
• 你可以根据自己的偏好留存或删除Cookie。您可清除软件内保存的所有Cookie,清除后您的相关信息即已删除。
• 我们将严格保证cookie技术的安全使用,不会给您带来不利影响。
3.2 日志文件
• 和大部分网站和移动应用一样,我们收集特定信息并保存在日志文件中。此类信息可能包括互联网政策 (IP)地址、互联网服务供应商 (ISP)、操作系统、日期/时间戳和/或点击流数据。我们不会将自动收集的数据链接到我们收集的关于您的其他信息之中。我们将严格保证技术的安全使用,不会给您带来不利影响。
3.3 网站分析
• 在访问网站过程中,我们会使用分析软件,以更好地了解网站的访问情况。此功能可能记录以下信息,如您使用该网站的频率、在网站内发生的事件、性能等数据。我们不会将存储于分析软件内的信息链接到您在网站中提交的任何个人信息。我们将严格保证技术的安全使用,不会给您带来不利影响。
四、 我们如何共享、转让、公开披露您的个人信息
1. 共享
由于我们的某些服务将由授权合作伙伴提供,一汽-大众可能会向合作伙伴等第三方提供您的个人信息。我们仅会出于合法、正当、必要、特定、明确的目的共享您的个人信息。
我们的授权合作伙伴无权将共享的个人信息用于本政策规定用途之外的任何其他用途,如要授权合作伙伴改变个人信息的使用目的,将再次征求您的授权同意。
在共享信息前,我们会对共享个人信息的第三方进行数据安全能力审核,与其签署严格的数据安全或保密协定,要求他们按照我们的说明、本隐私政策采取相关的保密和安全措施来处理上述信息。如涉及向以下提及的主体之外的其他方共享或提供您的个人信息,只有在获得您的明确同意后,我们才会分享或提供。
我们授权第三方共享您的个人信息包括以下情况:
• 数据分析服务提供商。包括Adobe、秒针系统。为提高产品或服务的质量及推广,我们会使用数据分析服务提供商提供的相关产品或服务,我们会将必要的个人信息传至该服务提供商,我们只针对群体数据进行画像分析,不针对独立个体进行直接用户画像分析;
为了数据统计和分析的目的,我们的平台集成合作方的秒针分析 SDK。秒针分析 SDK 将获
取您的页面浏览行为数据。若您想进一步了解秒针的个人信息保护政策,您可以前往
https://miaozhen.com/cn/privacy 进行查看。
为了数据统计和分析的目的,我们的平台集成合作方的Adobe Analytics SDK。Adobe Analytics SDK 将获
取您的页面浏览行为数据。若您想进一步了解Adobe Analytics的个人信息保护政策,您可以前往
https://www.adobe.com/privacy.html 进行查看。
• 一汽-大众的关联公司。因本网站业务的相关产品、研发、运营等职能分属在一汽-大众及关联公司,主要指一汽-大众销售有限责任公司,为了提升我们的产品或服务质量或向您提供全新的产品或服务,我们会在一汽-大众的关联公司内部共享您的个人信息,此关联公司仅限于与一汽-大众存在控制关系或从属关系的关联组织。
• 一汽-大众特许经销商。当您使用本隐私政策第二条所述的试乘试驾功能中,我们需将您的姓名、联系方式、及意向车型、意向时间的选择信息共享至您选择意向的一汽-大众特许经销商,用于为您提供试乘试驾服务。
2. 转让
我们不会将您的个人信息转让给除一汽-大众及其关联公司外的公司、组织和个人,但以下情况除外:
• 事先获得您的明确授权或同意;
• 根据法律法规、法律程序的要求或强制性的政府要求或司法裁定一汽-大众必须提供;
• 符合您签署的其它法律文件(如本条款)的约定而使用;
• 在涉及合并、收购或破产清算时,如涉及到个人信息转让,我们会要求新的持有您个人信息的公司、组织继续受此隐私政策的约束,否则我们会要求该公司、组织重新向您征求授权同意。
3. 公开披露
我们不会公开披露您的个人信息,以下情况除外:
• 获得您明确同意后;
• 基于法律的披露:在法律、法律程序、诉讼或政府主管部门强制性要求的情况下,我们可能会公开披露您的个人信息。
在以下情形中,共享、转让、公开披露个人信息无需征得个人信息主体的授权与同意:
• 与国家安全、国防安全有关的;
• 与公共安全、公共卫生、重大公共利益有关的;
• 与犯罪侦查、起诉、审判和判决执行等有关的;
• 出于维护个人信息主体或其他个人的生命、财产等重大合法权益但又很难得到本人同意的;
• 个人信息主体自行向社会公众公开的个人信息;
• 从合法公开披露的信息中收集个人信息的,如合法的新闻报道、政府信息公开等渠道。
五、 我们如何保存及保护您的个人信息
1. 保存地域
您的个人信息将储存于中华人民共和国境内。除您在境外使用一汽-大众产品/服务需要数据传输情形外,如需跨境传输,我们将会明确向您告知出境的目的、接收方、安全保障措施等情况并单独征得您的授权同意。
2. 保存期限
2.1 在用户使用本网站服务期间,我们会持续保存用户的个人信息。
2.2 当您申请删除个人信息或注销账户,我们将按照法律、法规规定的最短期限保留您的现有个人信息,在法律法规要求的最短保存期限内,我们将不再对您的个人信息进行商业化使用。当您的个人信息超出上述保存期限,我们将会对其进行匿名化处理。
3. 安全措施
一汽-大众会采取适当的符合业界标准的安全措施和技术手段存储和保护您的个人信息,以防止其丢失、被误用、受到未授权访问或泄漏、被篡改或毁坏。
3.1 我们将采取以下安全技术措施保护您的个人信息:
a. 数据传输过程中使用加密传输协议。
b. 严格控制数据访问权限,特别是对批量数据操作权限的控制和审查。
c. 对应用系统上线经过漏洞扫描、渗透测试等进行安全测试,并对相关风险进行整改;
d. 对数据的定期备份,及相关恢复可用性测试;
e. 建立数据安全监控和审计制度,进行全面的数据安全控制。
3.2 我们同时采取其他安全措施保护您的个人信息:
a. 建立公司保密及信息安全委员会,统一协调信息安全工作,推动各项信息安全活动,公司内部颁布个人信息保护规范。
b. 系统上线前或重大功能变更前对数据安全(包括用户个人信息数据)进行个人信息影响评估。
c. 与全体员工及服务外包人员签署保密协议,并严格按照工作职责分配数据访问权限。
d. 定期开展面向公司全体员工及外包服务人员的信息安全教育及培训。
3.3 安全事件处置
a. 为应对个人信息泄露、毁损、丢失等可能出现的安全风险,我们建立系统上线前的安全测试流程,以及内部处理流程(包括应急响应流程)和补救措施。
b. 一旦发生安全事件,我们将及时向您告知事件基本情况和风险、我们已经采取或将要采取的措施、您如何自行降低风险的建议等。
c. 我们将及时以推送通知、电话等方式将安全事件情况通知受影响的用户。当难以逐一告知用户时,我们将通过发布平台公告的方式发布警示信息。
六、 您的权利
一汽-大众非常尊重您对个人信息的关注,并为您提供了管理个人信息的方法。我们保障您对自己的个人信息行使以下权利:
1. 访问、变更您的个人信息
1.1 访问您的个人信息。您可以通过网站个人中心,访问您的个人账户资料信息。或您可以联系一汽-大众客服中心咨询相关信息(4008-171-666),我们将在30个工作日内回复您的请求。
1.2 更正个人信息。当您需要更新您的个人信息,或发现网站收集、存储的个人信息有错误时,您有权做出更正或更新。您可以通过网站个人中心-修改个人信息功能,自行更正或修改个人账号信息、修改密码、及变更手机号等。您可以联系一汽-大众客户服务中心(4008-171-666)咨询具体更正流程。您也可以随时发送电子邮件至(service@audi.cn)。我们将在验证通过后不超过30个工作日或法律法规规定期限内回复您的请求。
2. 改变您授权同意的范围或收回您的授权同意
我们将通过以下方式保障用户撤回同意的权利:
您可以联系一汽-大众客户服务中心(4008-171-666)或发送电子邮件至(service@audi.cn)更改您的授权同意。
当您撤回同意或授权后,我们将不再处理相应的个人信息,这可能导致我们无法为您继续提供撤回授权部分对应的服务。您撤回同意或授权,不影响撤回前基于您的同意开展的个人信息处理。
3. 删除您的个人信息
在以下情形中,您可以通过本隐私政策第十一条“如何联系我们”中所列的联系方式向我们提出删除个人信息的请求:
• 如果我们处理个人信息的行为违反法律法规;
• 如果我们收集、使用您的个人信息,却未征得您的同意;
• 如果我们处理个人信息的行为违反了与您的约定;
• 如果您不再使用我们的服务,或您注销了账户;
• 如果我们终止服务或运营。
若我们决定响应您的删除请求,我们还将尽可能同时通知从我们获得您的个人信息的实体,要求其及时删除,除非法律法规另有规定,或这些实体获得您的独立授权。当您从我们的服务中删除信息后,我们可能不会立即从备份系统中删除相应的信息,但会在备份更新时删除这些信息。
如果我们终止服务或运营,我们会至少提前三十个工作日向您通知,并在终止服务或运营后对您的个人信息进行删除或匿名化处理。
4. 账户注销
您可通过本隐私政策第十一条“如何联系我们”中所列的联系方式向我们提出账户注销的请求。
除法律法规另有规定外,注销账号之后我们将停止为您提供服务,
并根据本政策约定期限保存您的个人信息,保存期限届满后我们将对您的个人信息进行匿名化处理。
5. 申诉咨询及客户响应
为保障您及他人的个人信息安全,您可能需要提供书面请求,或以其他方式证明您的身份。我们可能会先要求您验证自己的身份,然后再处理您的请求。
我们将在15个工作日内做出答复。如您不满意,还可以过本隐私政策第十一条“如何联系我们”所列的联系方式向我们进行投诉。
如果您对我们的回复不满意,特别是您认为我们的个人信息处理行为损害了您的合法权益,您还可以通过以下外部途径寻求投诉或结局方案:向国家个人信息监管部门反映投诉、一汽-大众住所地有管辖权的法院提起诉讼;
对于您合理的请求,我们原则上不收取费用,但对多次重复、超出合理限度的请求,我们将视情收取一定成本费用。对于那些无端重复、需要过多技术手段(例如,需要开发新系统或从根本上改变现行惯例)、给他人合法权益带来风险或者非常不切实际(例如,涉及备份磁带上存放的信息)的请求,我们可能会予以拒绝。
在以下情形中,按照法律法规要求,我们可能将无法按照您的请求进行操作,但我们会在15个工作日内向您说明原因:
• 与国家安全、国防安全有关的;
• 与公共安全、公共卫生、重大公共利益有关的;
• 与犯罪侦查、起诉、审判和执行判决等有关的;
• 有充分证据表明个人信息主体存在主观恶意或滥用权利的;
• 响应您的请求将导致您或其他个人、组织的合法权益受到严重损害的;
• 涉及商业秘密的。
七、 我们如何处理未成年人的个人信息
一汽-大众重视对未成年人信息的保护。
我们的产品、网站和服务主要面向成人。如果没有父母或监护人的同意,未成年人不得创建自己的用户账户;如果您/您的监护人不同意本隐私政策的任何内容,您应当立即停止使用本软件。
如果我们发现在未事先获得可证实的监护人同意的情况下收集了未成年人的个人信息,则会设法尽快删除相关数据。
如果监护人发现我们在未获监护人同意的情况下收集了未成年人的个人信息,请通过本隐私政策第十一条“如何联系我们”所述联系方式联系我们,我们会设法尽快删除相关数据。
八、 您的个人信息如何跨境转移
原则上,我们在中华人民共和国境内收集和产生的个人信息数据,将存储在中华人民共和国境内。如需将您的个人信息进行跨境转移,我们将会单独征求您的授权同意;
九、 适用法律与争议解决
1. 适用法律
本政策的执行、解释及争议的解决均适用中华人民共和国法律,且不考虑任何冲突法。
2. 争议解决
您和一汽-大众就本政策内容或其执行发生任何争议的,双方应友好协商解决;如双方无法协商解决争议时,双方同意应将争议提交至被告住所地人民法院裁决。
十、 本政策如何更新
本政策将根据业务模式的调整或更新不定期进行修订,该等修订构成本隐私政策的一部分,并具有溯及力。
未经您的明确同意,我们不会削减您按照本隐私政策所享有的权利。我们会通过电子邮件、信函、电话、推送通知等方式告知您隐私政策所做的变更。
如发生重大变更,我们将会采取更具有提示作用的方式告知用户,包括但不限于发送邮件、推送通知、弹窗通告。
本政策所指的重大变更包括但不限于:
• 我们的服务模式发生重大变化。如处理个人信息的目的、处理的个人信息类型、个人信息的使用方式等;
• 我们在所有权结构、组织架构等方面发生重大变化。如业务调整、破产并购等引起的所有者变更等;
• 您参与个人信息处理方面的权利及其行使方式发生重大变化;
• 我们负责处理个人信息安全的责任部门、联络方式及投诉渠道发生变化时;
• 个人信息安全影响评估报告表明存在高风险时。
我们还会将本政策的旧版本存档,供您查阅。
本隐私政策在网站运营或提供使用期间有效,在业务永久停止运营或永久停止提供使用时失效,失效后我们依然将根据国家法律法规要求保护您个人信息安全相关权益。
十一、如何联系我们
如果您对本隐私政策有任何疑问、意见或建议,或您在使用一汽-大众产品或服务时,就您的个人信息的收集、使用、共享、访问、删除、更正等相关事宜有任何意见或建议,您都可以通过下列方式与我们联系。
客服电话:4008-171-666
奥迪在线客服(网页版)
邮箱:service@audi.cn
特别提示:一汽-大众提醒您,如您反馈的问题涉及您的个人信息,尤其是您的敏感信息,请您不要直接在电话或邮件中进行透露,我们将会在确保您个人信息安全的情况下与您进一步沟通。
部分情况下,为保障您个人信息的安全,我们可能需要您提供书面请求,或以其他方式证明您的身份。我们将在收到您的反馈并验证您的身份后15工作日内答复您的相关请求。
奥迪践行循环经济愿景
奥迪致力于让循环理念成为汽车价值链中不可或缺的一部分,并贯穿产品设计、采购、生产、营销、再利用的各个环节之中。。
由于地球资源有限,如何有效利用资源自然就十分关键。对此,奥迪循环经济专家Dennis Christian Meinen 表示:“建立材料闭环,可以有助于实现在经济发展的同时,降低资源消耗,减少对资源的依赖。”循环经济的目标,正是尽可能地延续产品与材料的价值
.jpg)
可回收性设计
奥迪始终着眼于产品的全生命周期。奥迪在每辆车的生产中,都采用了包括钢、铝等金属、塑料、电子和玻璃等多种材料。虽然多数材料早已可以进行充分回收再利用,但仍有一些材料常常只能降级回收。因此,奥迪希望能建立更多材料回收闭环,最大化地提高资源利用率。
早在汽车研发和设计阶段,即首批汽车出厂的数年前,奥迪就充分考虑到可回收的可能性。在“使用二次材料最环保(Materials not used in the first place protect the environment the most)”理念的引领下,奥迪致力于推进可持续产品研发,不断寻找灵感,探索提高可回收性、节约材料使用等问题的解决方案。另外,鉴于设计仍是客户购买奥迪的首要原因,奥迪也尤其注重可持续性与美学设计之间的平衡。
.jpg)
再利用或再加工
秉持建立闭环回收、发展循环经济的理念,奥迪将对达到使用年限的车辆零部件情况先做出判断,再进行合理处理。首次使用后的零部件不一定要经过回收后再利用。最理想的情况,就是无需进一步改造就可重新在其他地方利用,仅需简单的修补就足够。例如,变速器就是加工再利用的理想选择。另外,电池再加工后也可用于储能设备。在闭环再加工或再利用过程中,零部件将被回收,用于新部件生产,而使用再生材料的一大优点就是可节约生产新材料(即原生材料)所需的宝贵资源与能源。
.jpg)
铝闭环
25余年以来,铝材料被越来越广泛地应用于汽车制造中。汽车制造为能源密集型生产,如何对铝材料进行有效利用尤为重要,而只有再生铝加工和利用的质量与原生铝质量相同时,才能称得上是建立起了铝闭环。如今通过铝闭环系统,奥迪及其供应商已实现铝废料回收,并使回收质量达到原生铝水平。自2017年起,奥迪冲压工厂成功引入铝闭环系统,2021年减少超过195,000吨的二氧化碳排放。如今,奥迪的内卡苏姆工厂、英戈尔施塔特工厂、杰尔工厂(自2021年开始)以及布拉迪斯拉发的多品牌联合生产基地,均已开始实施铝闭环。奥迪也是首家获颁“全球铝业管理倡议监管链证书(the Aluminium Stewardship Initiative’s Chain of Custody certificate)”的汽车制造商。
.jpg)
塑料的化学回收
奥迪始终在探索如何将循环经济理念应用于更多材料。其中,对多种塑料垃圾的回收尤其具有挑战性。平均而言,目前每辆汽车拥有约250公斤的塑料零部件,而进行回收的其中一种方法,就是将这些部件与其他材料分开、粉碎,再重新加工成塑料颗粒。
但在回收复合材料中的塑料时,因材料中含有各种粘合剂、涂料和填料(如玻璃纤维),机械性的回收塑料方式往往无法奏效。此外,塑料质量也将随着机械加工步骤的增多而相应下降。因此,以这种方式回收的塑料不适用于汽车生产,尤其是与安全性相关的关键零部件的制造。
为此,奥迪携手卡尔斯鲁厄理工学院(KIT)和行业合作伙伴,致力于推出一种新的回收方法。回收塑料废料可加工成热解油,代替石油作为生产高质量塑料零部件的原料。现有研究表明,由热解油制成的部件能具有与原生材料相同的高质量。这种闭环式塑料回收可有效节约能源,优化采购流程。据预估,回收的再生材料将有一半以上可再度用于汽车生产。
.jpg)
由再生材料制造的零部件
此外,为节约资源,越来越多的奥迪汽车零部件由再生材料——即在回收过程获得的加工材料制造而成,除了减排之外,更是为了让材料的利用更加经济高效。将来,奥迪计划不断提高再生材料的应用率。例如,用单一品种的材料制造椅套,以便于后续回收再利用。
奥迪Q4 e-tron中有27个部件是由工业生产废料等再生材料制成,这些塑料部件尤其需要在汽车全生命周期内满足严格的耐热性、尺寸稳定性和质量要求。外观设计方面,再生材料也用于对机械精度要求极高的部件,诸如总成支架、前大灯或保险杠外壳的连接部件等。此外,前大灯支架、轮拱内衬、挡泥板罩、地台装饰件和车轮扰流板也都由再生材料制成。
.jpg)
PET瓶的回收利用
在奥迪Q4 e-tron内饰部分,再生材料主要用于绝缘和滤震材料。除此之外,许多肉眼可见的配置中也都含有再生材料,例如地台垫和行李厢内衬部件等。在奥迪S系列车型的内饰中,Dinamica超细纤维材料结合人造革制成了运动座椅套。45%的Dinamica材料由提取自PET瓶、旧纺织品或纤维残余物的聚酯纤维制成,但其外观和触感与绒面革相同。与超细纤维质量相比,Dinamica材料采用无溶剂生产,更有利于环境保护。
奥迪e-tron GT的地毯和脚垫采用由100%再生尼龙纤维组成的Econyl材料制成。这些纤维来自生产废料、纺织物、地毯废料或旧渔网。运动型座椅plus可选配黑色无皮革设计套件。该套件椅套或采用人造革与纺织材料Kaskade的组合,或采用人造革与超细纤维Dinamica组合的混合材料。总体而言,无论是哪种组合形式,该椅套都主要是由提取自PET瓶、纺织品或纤维残余物的聚酯纤维等材料制成,生产一个Kaskade椅套就使用了119个PET瓶。
第四代奥迪A3首次采用由再生材料制成的椅套,再生材料的使用率高达89%。奥迪A3每个座椅可使用多达45个容量为1.5升的PET塑料瓶。全车地毯还可再利用62个回收的PET塑料瓶。此外,奥迪A3内饰其他组件如绝缘材料、后备厢侧板、后备厢地板和后备厢垫等,也越来越多地由再生原材料制成。
.jpg)
低碳铝轮辋
作为试点项目的一部分,奥迪正在为奥迪e-tron GT采购由低碳铝制成的20英寸轮辋。这种环保材料是凭借创新的冶炼工艺制造而成,可释放氧气,而不会直接产生碳排放。此外,车轮在德国的生产流程中也应用了100%的绿色能源。
.jpg)
车窗玻璃回收闭环
奥迪及其合作伙伴在建立车窗玻璃材料的闭环回收系统方面正走在行业前沿。目前,奥迪已携手合作伙伴Reiling Glas Recycling、圣戈班玻璃(Saint-Gobain Glass)和圣戈班汽车玻璃系统(Saint-Gobain Sekurit)启动了玻璃回收试点项目。为将损坏的汽车玻璃转化为可回收材料,并重新投入新车生产,奥迪和其合作伙伴制定了一套专业化的多阶段回收流程:首先,利用创新的回收工艺,将受损玻璃打碎成小块;然后,清除所有非玻璃杂质,如胶水残留物等;由此产生的玻璃颗粒被熔化,并制作成新的平面玻璃;最后,这些玻璃板通过进一步制作变成新车窗。若该试点项目成功,回收生产的新车窗将用于奥迪纯电车型。
回收受损玻璃意味着减少车窗生产过程中能源和原材料的消耗,使用回收加工材料最终也可减少对诸如石英砂等原生原料的需求。
这项玻璃回收项目充分表明,通过创新技术可建立起更多材料回收闭环,助推循环经济。此外,现有的材料闭环也可不断优化。总体而言,循环经济的潜力仍十分巨大。
展望未来
对奥迪而言,发展循环经济的重要性正日益显著。奥迪对可持续发展的承诺也体现在方方面面,例如在设计中所采用的集美观、高质量和可持续性于一体的全新材料。奥迪始终勇于在创新技术领域不断突破,未来也将不断改进现有的材料闭环回收系统,探索更多循环经济的实践与应用。
(*注: 文中所提车型均为奥迪海外车型)。
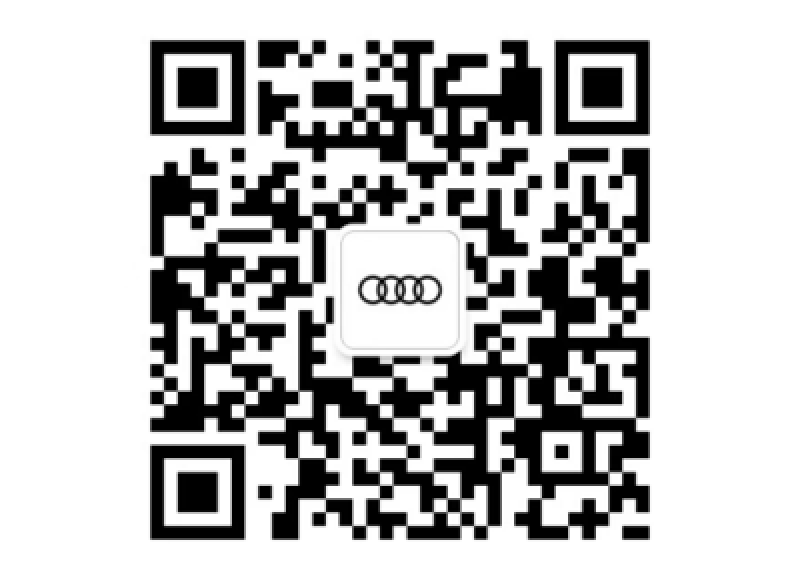